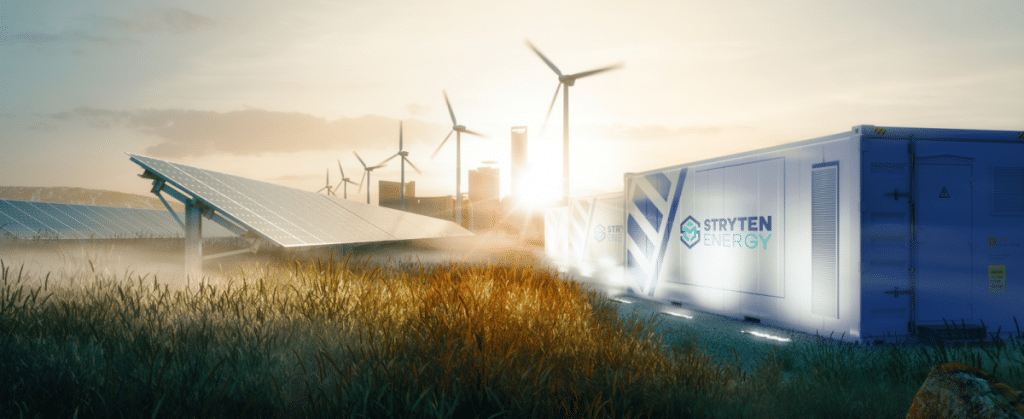
Lead batteries are a vital part of the transition to clean sources of energy.
The U.S. has ambitious goals to create a carbon pollution-free power sector by 2035 and a net-zero emissions economy by no later than 2050. The Department of the Interior has committed to deploying 30 gigawatts of offshore wind energy by 2030, with a target goal of permitting at least 25 gigawatts of onshore renewable energy by 2025. The cost for utility-scale solar power has declined 82 percent since 2010, and the costs for onshore and offshore wind have declined 39 percent and 29 percent, respectively.
According to the International Energy Agency, global electricity demand is expected to increase by an average of almost three percent a year from 2022 to 2024. The agency expects renewable energy sources to serve more than 90 percent of the net demand growth during this period.
But while we use more renewable energy sources, they aren’t always available, and we still rely heavily on fossil fuels to power our lives. The demand for energy is also on the rise making long-duration energy storage powered by a wide variety of battery technologies critical.
Lead batteries have operated efficiently behind the scenes to provide dependable energy storage to a number of industries and applications for over 160 years. Today, they have been overshadowed by new battery chemistries such as lithium. It’s time for the lead battery industry to shine the spotlight on what can be accomplished with additional funding for research to unlock the greater potential, greater investments in advanced manufacturing, defined battery usage standards, and a continued focus on sustainability.
Funding Additional Research to Expand Capacity
Investments in research and development are a key aspect of the Department of Energy’s (DOE) Energy Storage Grand Challenge (ESGC). The ambitious cost target for advanced lead battery technology is $35/kilowatt-hour (kWh), based on the untapped potential in this chemistry. Costs need to come down as utilities need to integrate the variable power from renewable energy such as wind and solar into the grid.
Researchers at the Lead Battery Science Research Program, alongside the DOE’s Argonne National Laboratory, have been working to study reactions within lead batteries in real-time. In addition to studying reactant crystals, researchers are also examining the effects additives and contaminants have on performance. We need to examine every element of the battery – anodes, cathodes, separators, electrolyte, etc. – to maximize capacity and extend life. We need to look at all of the material that goes into the production of the battery to ensure every component adds value.
Investing in Advancing Manufacturing to Meet Increasing Demand
Domestic manufacturing is critical to our economy and national security. The U.S. lead battery industry has an annual economic impact of $26.3 billion. For every $1.00 spent in manufacturing, there is a total impact of $2.68 on the overall U.S. economy. North American manufacturers meet more than 90 percent of domestic demand for lead batteries. This domestic sourcing minimizes the impact of foreign trade disruptions.
The Bipartisan Infrastructure Law provides over $3 billion in funding for domestic battery manufacturing and supply chains. The roadmap for the ESGC also includes accelerating the transition from R&D to commercialization, focusing on ways to manufacture technologies at scale competitively.
Investments should also be made in the people working in the plants. As manufacturing becomes even more sophisticated, the demand for skilled workers will continue to increase. U.S. manufacturing is expected to have 2.1 million unfilled jobs by 2030.
A growing number of manufacturing jobs will also require experience with digital technologies and digital systems. The increasing reliance on robotics and automated processes is creating more jobs within manufacturing. Companies need workers who understand robotics, artificial intelligence and data analytics. They need technicians who can program and repair that sophisticated equipment.
As manufacturers invest in their plants, they should also strive to advance the skills of their people to ensure they are ready for the increasing digitization and automation of manufacturing processes. Increased investments in manufacturing processes and a highly-skilled workforce will help ensure lead battery manufacturers are able to produce the batteries that will supply that necessary capacity to improve the efficiency of renewable energy sources.
Implementing Lead Battery Usage and Maintenance Standards
Lead batteries are the silent workhorse, generating the power demanded of them. They are used and abused until end of life, then recycled to build a new lead battery.
Lithium batteries, on the other hand, tend to have more defined parameters regarding the usage that the battery system can tolerate. The depth of discharge is specified, and users are prevented from pushing the battery beyond these limits. The lead battery industry should work towards a similar standard for depth of discharge or a certain number of kilowatt hours to ensure the batteries operate at peak efficiency.
Lithium battery systems also include a battery management system that calculates the remaining charge, monitors the battery temperature and reports the data to external devices. As we ask for more performance from lead batteries, we need to be more diligent in defining appropriate use and proper maintenance. Power electronics can monitor that performance to maximize useful life, allowing thousands of cycles rather than hundreds.
Elevating the Message About Lead Battery Sustainability
Sustainable energy is defined as “meeting the needs of the present generations without compromising the ability of future generations to meet their own needs.” This definition should apply to both energy sources and the materials used to produce energy storage solutions.
The lead battery industry has a strong story about the sustainability of lead batteries that is unique in the energy storage space. Nearly 100 percent of lead can be recycled and infinitely reused without any loss of future performance capacity. Even though the U.S. is one of the leading producers of lead globally, over 80 percent of lead demand is met by North American battery recyclers. This domestic footprint minimizes potential supply chain disruptions and ensures recycling is done in an environmentally conscious way.
Lead is also the most recycled consumer product, with a 99 percent recycling rate. Recycling keeps more than 130 million lead batteries out of landfills each year. Approximately 80 percent of a lead battery consists of recycled materials, which include lead and plastic components. The lead battery industry must strive to continually improve the recycling process to maximize the recycled materials and minimize the carbon footprint.
By comparison, the recycling rate for lithium batteries is only about 5 percent. The lack of a robust recycling process is one of the drawbacks of lithium battery systems. The Environmental Protection Agency (EPA) is currently soliciting feedback to develop best practices on the end-of-life management of batteries in order to increase the recovery of critical minerals while recognizing that lead batteries are already recycled at a high rate.
We must continue to share the success of the lead battery industry’s circular economy model with policymakers, customers and consumers. As the processes for recycling other battery chemistries mature, our industry may need to step up to provide access to our battery collection and transportation network footprint or potentially expand our recycling capabilities to accommodate other chemistries.
Bringing Lead Batteries into the Spotlight
Lithium has received significant attention and support from the DOE. A $5 million workforce initiative will support training programs and partnerships between the Department of Labor and the AFL-CIO for the domestic lithium battery supply chain. Lead battery manufacturers have just as much to contribute to achieving net-zero emissions goals, with a well-defined manufacturing footprint and dedicated workforce.
The lead battery industry is primed to be at the forefront of the energy storage landscape. The demand for energy storage is too high for a single solution to meet. Lead batteries already have lower capital costs at $260 per kWh, compared to $271 per kWh for lithium. But the price of lithium batteries has declined 97 percent since 1991.
In order to become more cost-competitive, we need to capitalize on research findings and advanced manufacturing, and continue to share the sustainability success story. Lead batteries are a vital part of the transition to clean sources of energy.
Mike Judd, President and Chief Operating Officer, Stryten Energy