In this article, Jeremy Furr, Senior Vice President of Strategic Sourcing, shares his insight on the importance of a domestic supply chain.
- Overall, it seems that the supply chain has returned to some normalcy. What lessons do you think have been learned from the pandemic?
It’s an interesting time for the supply chain. I have often asked, “Are things going back to where they were six years ago, or are some changes here to stay?”
We had gotten comfortable with just importing goods and materials with few issues. The container arrived from Europe or Asia, and if you kept the pipeline in order, everything went smoothly. I don’t think anyone could have imagined having five or six dozen container ships backed up at the ports of Los Angeles and Long Beach. At the time, many companies said they would never extend their supply chains again, but now you see some going back to China.
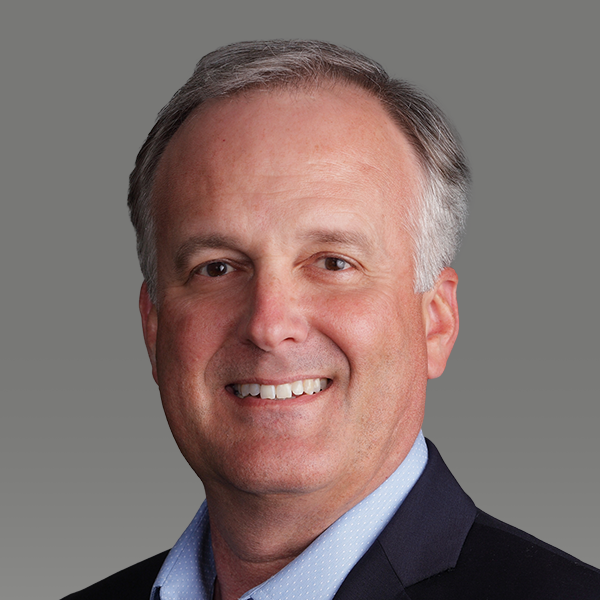
Jeremy Furr, Senior Vice President of Strategic Sourcing
We know having a long supply chain is risky, so a focus should be on risk mitigation. We cannot rely on single, sole-sourced imports. Drought in the region disrupted passage through the Panama Canal. Houthi fighters based in Yemen have been targeting ships in the Red Sea, which has decreased traffic in the Suez Canal by 66 percent. This volatility directly impacts ocean freight prices and total transit times as carriers reroute around Africa via the Cape of Good Hope.
There needs to be a domestically sourced option. Ideally, the primary source should be domestic, but having a domestic alternative is imperative.
- Inflation has also eased somewhat in the past year. What impact has that had on the supply chain?
The average inflation rate for 2023 was 4.1%, significantly down from 8.0% in 2022, but we’re still not at the 2% target. Interest rates have remained steady since July 2023. However, the Federal Reserve has scaled back its forecast of three rate cuts to just one as inflation began to creep up in the first half of 2024. Officials now estimate the federal funds rate may be in the range of 5-5.25% by the end of the year.
If you look at commodity markets, many are in much better shape. For example, HRC steel was up to almost $1.00/lb. Now, it’s approximately $0.35/lb. Like everything else, prices aren’t likely to return to where they were, but at least they’ve gone down.
It will take time for the impact of all these factors to trickle down to the consumer. In response to market volatility (both pricing and availability), many companies locked in prices for several years. While they may be overpaying now, it was a necessary business decision to allow accurate budget forecasts and to ensure delivery.
- One objective of the Inflation Reduction Act (IRA) passed in August 2022 was investing in domestic energy production while promoting clean energy. What has this provision done for supply chains in the battery industry?
Nearly half of the bill’s funds, $369 billion, are going toward efforts to improve energy security. Many of the strategies focus on supporting U.S. manufacturing and assisting corporations in the shift to cleaner sources of energy. The IRA’s benefits will be accessible through tax credits offered throughout the supply chain.
With this increased emphasis on energy security and the domestic production of tools to capture renewable energy, there will also be an emphasis on the tools that store this energy. The IRA’s provides a 30% investment tax credit to stand-alone energy storage systems, as well as incentives for domestic supply chain and manufacturing capacity.
In the battery industry, we must consider where to focus our efforts. Although lithium is often considered the predominant chemistry for these storage systems, much of the supply is used by the electric vehicle market, both for consumer and warehouse vehicles such as forklifts. There are also significant supply chain concerns surrounding lithium since approximately 65% of lithium processing capacity is held by China.
Over the next five years, the U.S. is expected to increase capacity more than ten times, moving into second place. Despite all the investments to compete, China is projected to remain in that dominant position. The U.S. has imposed significant tariffs on Chinese electric vehicles, semiconductors, battery components, critical minerals and more across sectors that are strategic to national security. We must ensure countries of concern do not negatively impact our supply chains.
- Are other battery technologies available to power clean energy storage systems?
The Department of Energy (DOE) has identified several battery chemistries to meet this need. Lead is a fit for shorter duration energy storage and is already available in abundance. According to the EPA, lead batteries have a nearly 100% recycling rate and are the most recycled consumer product in the U.S. The lead from lead batteries can also be infinitely recycled with no loss of performance.
Battery Council International is working with major battery manufacturers and researchers to reach the full potential of lead batteries and enhance battery performance efficiency. The Consortium for Lead Battery Leadership in LDES, funded by a $5 million DOE award, will conduct pre-competitive research to develop lead batteries capable of 10+ hours of storage with a pathway to $0.05/kWh Levelized Cost of Storage by 2030.
The vanadium redox flow battery (VRFB) is another chemistry available for long-duration applications. VRFBs offers a near-infinite lifecycle with proper maintenance. The VRFB electrolyte can last 20 years or more decades before it begins to lose storage capacity. Vanadium electrolyte typically constitutes 40-60% of the system cost, representing a key cost reduction to help rapidly scale the U.S.-based production and commercialization of VRFBs.
The DOE has identified flow batteries as well suited for applications such as utility-scale energy storage, microgrids and renewables integration. Up to $20 million has been set aside for research and development to improve the manufacturing processes of mid-sized flow battery systems. Recent DOE awards have gone to Project VITALITY, a microgrid project to demonstrate the benefits of VRFBs at commercial and industrial scale, and the SAVES Project to help rapidly scale the US-based production and commercialization of VRFB components and systems.
Establishing a domestic supply chain and manufacturing ecosystem for VRFBs is critical to meeting the country’s energy security and resilience goals. More DOE funding for non-lithium batteries is needed to support U.S.-based companies working to bring this technology to market.
- How does a domestic supply chain help the U.S. achieve energy security?
A lot is said about energy security, but we must consider energy independence. Both are essential in the transition to clean energy sources. We can’t have security without independence.
Energy security is about having continuous access to reliable sources of power. We must capture all available energy generated by traditional and renewable power sources. Energy storage systems, powered by advanced battery technology, ensure nothing goes to waste that can be used later when energy demand peaks.
Energy independence is just as critical. Reliance on imports for critical minerals can lead to supply chain disruptions, as we saw during the pandemic. These imports also have serious national security implications. Chinese manufacturers account for over 60% of the global market distribution of lithium batteries. We want to ensure the materials we need to power our grid and protect our critical infrastructure are not subject to foreign interference.
Energy independence means strengthening domestic manufacturing to minimize these disruptions and bolster national security. The Bipartisan Infrastructure Law includes $3.1 billion in funding to build more batteries and components in America and shore up domestic supply chains.
- Why is sustainability within the domestic supply chain important?
Sustainability within the supply chain goes back to energy security and energy independence. Maintaining control of the critical materials protects the integrity of the supply chain. Economically recycling and extracting critical minerals for many battery chemistries continues to be a challenge. With the majority of lithium batteries produced abroad, the U.S. is vulnerable to supply chain disruptions for this technology. One advantage to domestic lithium recycling is the potential to advance lithium manufacturing by having raw materials within the domestic supply chain.
The lead battery industry is a model for other battery chemistries to responsibly design, use, recycle and remanufacture materials. Even though the U.S. is one of the leading producers of lead globally, North American battery recyclers meet over 80% of lead demand. This domestic footprint minimizes potential supply chain disruptions.
There is still room for improvement. Some lead batteries are still sent outside North America for processing and remanufacturing. Exporting batteries for recycling, then importing finished batteries from foreign manufacturers creates unnecessary costs.
Concerns also exist about how the materials are handled once they leave our shores. U.S. battery manufacturers and recyclers follow some of the most comprehensive worker safety and environmental controls in the world. These standards protect people in the plants, the local community and the environment.