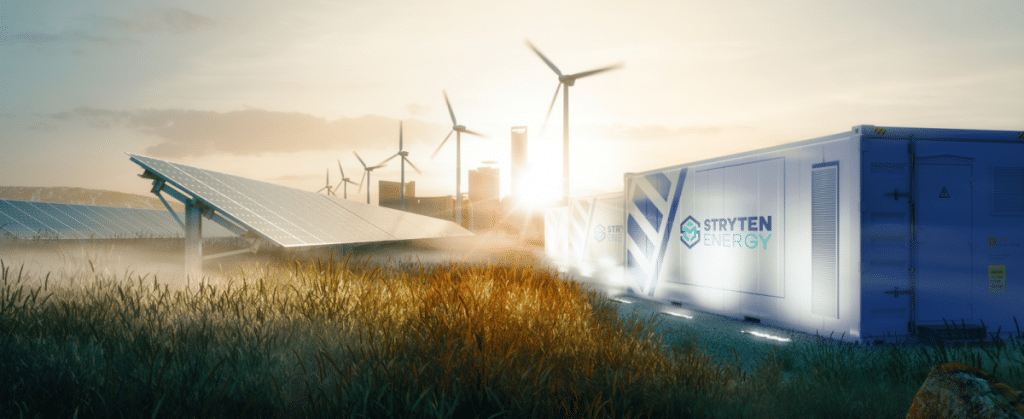
Advanced lead, lithium and vanadium battery chemistries will each play key roles in building more sustainable energy supply chains.
Domestic energy resilience is an important topic across the U.S. right now. The nation’s grid infrastructure is aging, and power consumption is expected to reach record highs. Utilities have almost doubled their forecast of the additional energy needed to meet the growing demands of manufacturing, data centers and EV charging stations.
Fossil-fuel power plants are facing increasingly strict environmental regulations. More than 200 coal plants have closed in the past decade. Operators plan to retire 15.6 gigawatts (GW) of electric-generating capacity this year, mostly natural gas-fired and coal-fired power plants. At the same time, 19 GW of solar capacity was added in 2023.
As coal and gas plants that provided consistent power are retired, and more renewable energy resources come online, we need proven back-up energy sources to help bridge the gap in supply and demand when electricity can be stored during peak hours of production for use at times with lower energy generation.
Much of the conversation is focused on how to leverage commonly available battery chemistries to create more battery energy storage systems (BESS). Lead has long been a reliable option with a diverse range of BESS use cases already in operation, and lithium, while already in demand for EVs and hybrid vehicles, could also play a role.
However, it’s going to take an even wider range of chemistries, including some nearing commercialization and some still in development, to nearshore our energy supply chain and give the U.S. a sustainable source of energy security.
Three trends in particular give us better insight into what the future of BESS might look like:
Trend #1: The ongoing battle of cost vs. performance
Lithium batteries come with plenty of pros. The chemistry is lightweight with high energy density. However, its supply chains are lengthy. While the U.S. is working to establish a domestic lithium battery supply chain, today lithium processing and battery manufacturing are heavily reliant on China. In Q4 2022, more than 85% of U.S. lithium-ion battery imports came from Chinese manufacturers.
Additionally, as manufacturers leverage lithium for long-duration energy storage, they’re finding some of the chemistry’s qualities – relatively short cycle life compared to other emerging chemistries, and restrictions created by power purchasing agreements – mean it isn’t always the right fit for their needs. Lithium is essentially a short-duration solution. To use it for long-duration needs, businesses must purchase and connect multiple lithium battery systems, a less viable commercial option as more EVs are manufactured and competition for the supply of lithium intensifies.
Utilities that enter into a lithium battery power purchasing agreement have also discovered the chemistry’s properties make it difficult to operate within the agreement’s parameters. The battery owner might require that the battery remain at a 50% state of charge, forestalling the lifespan reductions caused by full discharge. However, that approach leaves the business unable to use the battery as often as needed.
There are other, newer solutions that pose less of a roadblock, such as vanadium batteries, one of today’s emerging technologies with near infinite cycle life.
Trend #2: Vanadium fills the energy storage gap
Vanadium, while better suited for long-duration energy storage than lithium, comes with its own set of challenges in establishing a reliable supply chain. Now that manufacturers have proven vanadium’s usefulness as a battery chemistry, efforts will begin to build demand to a point at which mines are willing to carry the financial risk of investing in scaling up vanadium mining.
Currently, vanadium pricing typically rides construction market swings, reinforcing steel is vanadium’s primary use case. Mines want to avoid supplying too much vanadium and driving prices too low. As the chemistry reaches a more consistent demand within the energy storage industry, its pricing will be less prone to fluctuation. Market projections estimate that demand for vanadium to power vanadium redox flow batteries (VRFBs) will grow at a CAGR of approximately 56.7% through the rest of the decade, with even greater growth in the 2030s.
The supply and demand economics are challenged by consolidation and control of the vanadium market by countries of concern. Ensuring vanadium supply is available from friendly countries is a critical factor in establishing a domestic supply chain to meet the growing demand for VRFBs in the U.S.
Ultimately, the long duration and long life of VRFBs makes the work to scale U.S.-based supply chains worth it. Vanadium batteries can function for more than two decades without the electrolyte losing capacity, and the electrolyte is infinitely recyclable, making it a sustainable energy storage technology for generations to come.
Trend #3: A solution for critical needs – but smaller footprints
There are situations where a VRFB’s size makes it incompatible with smaller footprints. At the moment, VRFBs are mostly delivered in containerized solutions – an easily available form factor – but could one day look more like a chemical plant.
A lead BESS is often the right solution for smaller implementations. Lead is the “workhorse” of the energy field, as a safe and reliable battery technology. Lead batteries also have a robust circular economy – nearly 100% of a lead battery can be recovered to make new batteries at end-of-life. Because of the strength of lead batteries as a reliable energy storage solution, they are widely used for backup power in multiple use cases, including telecommunications and utilities, network operations and data centers, microgrids and residential solar.
A brief outage for smaller commercial or industrial operations, such as food manufacturing facilities, can cause tens, or even hundreds, of thousands of dollars in waste. Lead BESS would be the right technology to keep these operations up and running.
These systems are also capable of integrating renewable energy sources into the grid, and helping businesses integrate more sustainable energy generation into their operations. A project in Atlanta is underway to demonstrate how a lead BESS can help keep a community center running during periods of prolonged power outages, up to three days, ensuring critical supplies are kept at the right temperature, and residents have access to clean water and electricity.
Lead BESS technology could also play a key role in stabilizing the EV charging market, helping stations move away from variable electricity costs. By charging batteries in off peak times when costs are low, charging stations have access to a reservoir of energy during peak demand periods such as late afternoon and evening. This creates a more consistent cost structure. Pairing the EV charger with a battery and solar offers even greater savings potential.
Finding the right BESS solution for the right use cases
As the need for more BESS solutions climbs, lead, lithium and vanadium battery chemistries will each play key roles in building more sustainable energy supply chains. Lead’s recyclability means there’s a consistent supply of the material for building BESS. Lithium is a viable option for shorter durations. And vanadium, while not yet widely implemented, promises to offer long-duration energy storage on a large scale.
Each chemistry offers unique benefits that make it fit for different applications. A range of battery chemistries will be needed to meet the evolving energy storage needs of the U.S. to provide energy resilience and security.
Scott Childers, Vice President, Essential Power