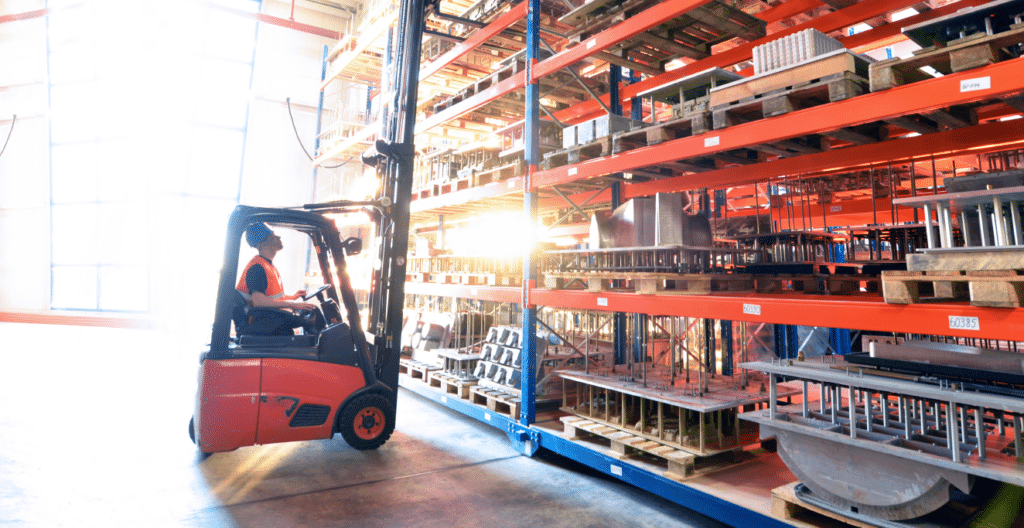
Choosing a fast charger is critical decision. A true fast charger is part of an engineered system matching the right-size battery to the right-size charger, allowing a forklift to run through multiple shifts using only one battery.
If you’re thinking about switching your motive power fleet from battery changing or liquid propane to fast charging, this checklist will help you pick a fast charger capable of powering your high-demand, multi-shift operation.
Control
First, make sure your fast chargers include real-time temperature control and correction. Fast charging is more than just charging fast – it’s about precise control of the charge curve. Minimizing heat, off-gassing and battery wear require precise control. If your charger doesn’t shut off when the battery gets too hot, it may not be engineered for the demands of fast charging.
Monitoring
When choosing a fast charger, be sure the chargers can monitor the battery’s voltage and current to prevent overheating and maximize throughput. Throughput is the amount of energy that a system needs to power each shift. Think of a battery like a gas tank, with electricity as the fuel measured in ampere hours (AH) instead of gasoline. By combining the ability to quickly “fill” a battery with constant monitoring, a true fast charger allows an operation to maintain maximum throughput.
Modeling
Be sure the up-front application modeling includes worst-case scenarios, peak season operating needs and growth projections. Simulation software can model and compare aspects of chargers, including throughput limits and charge rates. By properly sizing the system, power can be delivered consistently and efficiently, even during peak demand time.
Equalization
Look for an intelligent management system that automatically recognizes the need to finish and equalize when choosing a fast charging system. Fast chargers should make it easy for operators to perform this weekly activity.
Start Rate
For industrial motive power batteries, there are three levels of charging:
- Conventional – used in both battery changing and single-shift operations, conventional charging returns 16-18 amps per 100-ampere hours, for a charge rate starting at 16%-18%. Conventional charging typically requires 8 hours of charge time followed by 8 hours of cooling prior to use.
- Opportunity – used by single-shift and light-demand 2-shift operations, opportunity charging returns 25 amps per 100-ampere hours, for a charge rate starting at 25%. Opportunity charging avoids the need to change batteries, but may not deliver enough energy for high-demand operations. Some opportunity chargers are called “rapid” or “quick.”
- Fast – used by medium- to high-demand 2- and 3-shift operations, fast charging returns 40-50 amps per 100-ampere hours, for a charge rating starting at 45%-50%. This allows a forklift’s battery to be charged in short bursts during breaks, providing enough energy for all-day, heavy-duty lift truck usage. This is a true fast charger.
Flexibility
Finally, the charger should be truly flexible, accommodating a wide range of battery voltage and AH configurations. This offers the ultimate in cross-compatibility among forklifts in the existing fleet and helps to inform future decisions as forklifts are being replaced.
In conclusion, there are several considerations when choosing the fast charging system best for your operation.